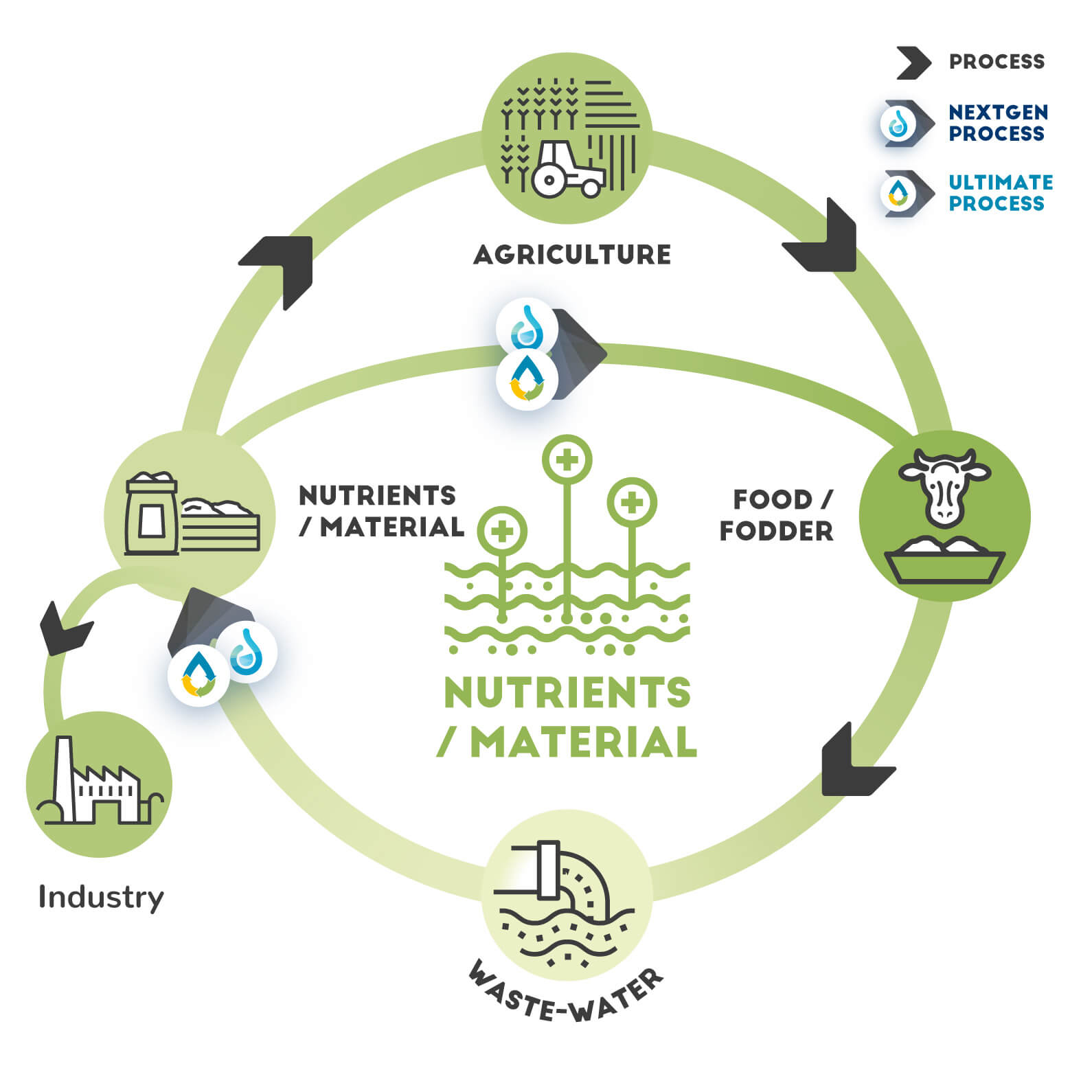
Description of the technology
Electrochlorination (EC) is a water treatment process that utilizes electricity to produce sodium hypochlorite (NaOCl) or chlorine (Cl2) from saltwater (brine). The process involves passing a direct current through an electrolytic cell containing brine solution (Badruzzaman et al., 2009). The electrolysis of brine leads to the formation of sodium hypochlorite, which is a powerful disinfectant commonly used in water treatment for disinfection purposes. The generated sodium hypochlorite can be directly dosed into the water to eliminate harmful microorganisms such as bacteria, viruses, and algae.
The electrochlorination process is enabled due to the presence of the electrolytic cell that will host the electrochemical reactions necessary for chlorine production. Typically constructed from robust and corrosion-resistant materials such as titanium, the electrolytic cell includes an anode and a cathode immersed in a brine solution. With the application of a direct electric current, the electrolysis of the brine solution is carried out. At the anode, chloride ions (Cl-) undergo oxidation, leading to the formation of chlorine gas (Cl2) and releasing electrons. Concurrently, at the cathode, water molecules (H2O) are reduced to produce hydrogen gas (H2) and hydroxide ions (OH-). Meanwhile, sodium ions (Na+) from the salt remain in solution, contributing to the formation of sodium hydroxide (NaOH) (Choi et al., 2013). This interplay of chemical reactions within the electrolytic cell leads eventually to the production of two primary disinfectants: chlorine gas and sodium hypochlorite. Both disinfectants can be collected for various industrial applications, including water treatment and sanitation processes.
Electrochlorination offers several advantages over traditional chlorine production methods. By generating chlorine-based disinfectants onsite, the need for transporting and storing hazardous chemicals is significantly reduced, mitigating associated safety risks and logistical complexities. Moreover, the process affords greater control and flexibility in adjusting disinfectant dosage levels to meet specific water treatment requirements, thereby enhancing operational efficiency and efficacy.
Flow scheme of the technology
The overall chemical reaction for the formation of sodium hypochlorite (NaOCl) from salt (NaCl) and water (H2O) is (Mostafa et al., 2018):
Reaction at the Anode: 2Cl- → Cl2 + 2e-
Reaction at the Cathode: 2H2O + 2e- → H2 + 2OH-
Chemical reaction in Electrolyzer: Cl2 + 2OH- + 2Na+ → 2NaClO + H2
Fig. 1 Electrochlorination cell scheme.
On-site generation process flow includes as described in Figure 2 consists on:
- The softened water is supplied to the Electrolytic Cell and the Brine Tank.
- In the Brine Tank, salt and water are mixed to create a saturated brine solution.
- The saturated brine is diluted with softened water, and this diluted brine solution enters the Electrolytic Cell.
- An electrical current is applied to the Electrolytic Cell, which produces an oxidant solution.
- Hydrogen gas, a byproduct of the electrolysis process, is vented outside the system.
- The oxidant solution generated in the Electrolytic Cell is stored in the Oxidant Tank.
- A metering pump doses the oxidant solution from the Oxidant Tank into the treatment process.
- The On-Site Generator (OSG) is controlled by a level switch signal located inside the Oxidant Tank, which turns it on or off based on the oxidant solution level.
Fig. 2 On-site generation process flow of hypochlorite. Adapted from Electrochemical Generation. The Applications and scientific mechanisms of disinfectants generated onsite using salt, water and electricity. By Andrew Boal, Ph.D.
Technology requirements and operating conditions
Electrodes and cell design:
Regardless of the process type, the anode must meet specific requirements as it comes into contact with highly reactive oxidants. Initially, graphite electrodes were used, but later, electrodes made of platinum, diamond, and other materials were developed. Currently, the most common solution is the use of dimensionally stable anodes (DSA), consisting of titanium coated with a layer of metal oxides such as ruthenium, iridium, or titanium.
The cathode, which is in contact with hydroxide ions, poses less of a corrosion problem. While stainless steel electrodes may be suitable, energy considerations lead to the adoption of more advanced materials. The choice of electrodes also influences the optimization of current/voltage parameters by affecting the overvoltages required for activating the reactions and, consequently, the operating energy cost. For this reason, activated nickel-based cathodes coated with a catalyst containing nickel and platinum group elements are commonly used (Li et al., 2021).
In terms of the cell design, it is necessary to substantially decrease the thickness of the electrolytes for reducing the cell resistance. One approach is to reduce the distance between the electrodes while preventing gas blockage between the electrode and the membrane (Isidro et al., 2020).
Another solution is to change the positioning of the different components. In the simplest case, porous electrodes are placed directly in contact with the membrane, hence the term "zero-gap." A more complex setup can also be employed, where the membrane is placed in contact with the cathode using a mesh glued to it and connected to a cathode by an elastic metal element, ensuring electrical conductivity between the two cathode components (Belhadj Ammar et al., 2022).
Technology requirements and operating conditions:
In contrast with the conventional chlor-Alkali process, the electrolyte solution used in electrochlorination is more dilute to prevent excessive salt transport, but it must remain sufficiently concentrated to limit electrical resistance. The concentration of the electrolyte at the anode can range from 180–240 g/L to 1.65–3.5 g/L at a pH between 1.0 and 4.5 (Kim et al., 2021). Different aspects have been studied such as the influence of flow rate, NaCl concentration, electrolysis time, and current density on the solution's activity (Liao et al., 2007). Although the variations in parameters were small, recommended operational parameters are flow rate (10 mL/s), the range of salt concentration (0.2-3 g/L), and the highest current density (0.4 A/cm²).
Depending on the physical characteristics and operating conditions of the electrolytic cell, such as the distance between the electrodes and the applied voltage potential, it is possible to generate oxidants other than chlorine. These alternative oxidants can offer improved removal of microbiological contaminants from water and provide additional benefits. Once produced, the chlorine gas dissolves in water, forming hypochlorous acid (HOCl).
Implementation of safety protocols to handle both chlorine and hydrogen produced during electrolysis, including proper ventilation and monitoring systems.
Key performance indicators
Performance may vary depending on salt quality, water quality and water temperature.
Tab. 1 Typical KPI´s values for electrochlorination processes.
12.5% Bleach Equivalent per Kg de FAC |
8.5 L/kg FAC |
(Kim et al., 2021) |
Salt Conversion (SCE) |
3 kg salt/kg FAC 3.5 kg salt/kg FAC 4-4.5 kg salt/kg FAC 3.3 kg salt/kg FAC |
(MIOX, De Nora, Italy) [1]
(Di-nol, China) [2]
(Selcoperm, Grundfos, Denmark) [3]
(Hyprolyser, Gaffey, UK) [4] |
Energy Conversion (ECE) |
6.6 kWh/kg FAC 4 kWh/kg FAC 5.5-6.5kWh/kg FAC 5.6 kWh/kg FAC |
(MIOX, De Nora, Italy) (Di-nol, China) (Selcoperm, Grundfos, Denmark) (Hyprolyser, Gaffey, UK) |
FAC Concentration |
4500 mg/L± 1000 mg/L 8000 mg/L ±1000 mg/L |
(MIOX, De Nora, Italy) (Di-nol, China) (Selcoperm, Grundfos, Denmark) (Hyprolyser, Gaffey, UK) |
Operating range of salt concentration |
0.2-3 g NaCl /L |
(Belhadj Ammar et al., 2022) |
[2] https://www.di-nol.com/sodium-hypochlorite-generator-from-brine-solution/sodium-hypochlorite-disinfection-machine.html
[4] https://www.gaffeytechnology.com/products/standard/
Maintenance is an important element for this type of cells, using appropriately softened water and high quality salt are the two most important factors of such cell maintenance. Even under these conditions, though, electrochemical cells will develop scale over time. The design of pretreatments for circular economy schemes for brine valorization have to include the removal of elements that may affect the cell´s performance.
According to the literature, electrochlorination stands out as one of the most promising alternatives for disinfection (Shinde et al., 2023). It can be implemented as a decentralized system in remote areas, overcoming many challenges associated with chemical disinfection methods.Links to related topics and similar reference projects
Badruzzaman, M., Oppenheimer, J., Adham, S., & Kumar, M. (2009). Innovative beneficial reuse of reverse osmosis concentrate using bipolar membrane electrodialysis and electrochlorination processes. Journal of Membrane Science, 326(2), 392-399.
Belhadj Ammar, R., Ounissi, T., Baklouti, L., Larchet, C., Dammak, L., Mofakhami, A., & Selmane Belhadj Hmida, E. (2022). A new method based on a Zero gap electrolysis cell for producing bleach: concept validation. Membranes, 12(6), 602.
Boal, A. Electrochemical Generation. (https://www.macguireandcrawford.com/wp-content/uploads/Tech-Brief_Electrochemical-Generated-Disinfectants.pdf)
Choi, J., Shim, S., & Yoon, J. (2013). Design and operating parameters affecting an electrochlorination system. Journal of Industrial and Engineering Chemistry, 19(1), 215-219.
Khelifa, A., Moulay, S., Hannane, F., Benslimene, S., & Hecini, M. (2004). Application of an experimental design method to study the performance of electrochlorination cells. Desalination, 160(1), 91-98.
Li, K., Fan, Q., Chuai, H., Liu, H., Zhang, S., & Ma, X. (2021). Revisiting chlor-alkali electrolyzers: From materials to devices. Transactions of Tianjin University, 27, 202-216.
Isidro, J., Brackemeyer, D., Sáez, C., Llanos, J., Lobato, J., Cañizares, P., ... & Rodrigo, M. A. (2020). Testing the use of cells equipped with solid polymer electrolytes for electro-disinfection. Science of the total environment, 725, 138379.
Kim, S. K., Shin, D. M., & Rhim, J. W. (2021). Designing a high-efficiency hypochlorite ion generation system by combining cation exchange membrane aided electrolysis with chlorine gas recovery stream. Journal of Membrane Science, 630, 119318.
Liao, L. B., Chen, W. M., & Xiao, X. M. (2007). The generation and inactivation mechanism of oxidation–reduction potential of electrolyzed oxidizing water. Journal of Food Engineering, 78(4), 1326-1332.
Mostafa, E., Reinsberg, P., Garcia-Segura, S., & Baltruschat, H. (2018). Chlorine species evolution during electrochlorination on boron-doped diamond anodes: In-situ electrogeneration of Cl2, Cl2O and ClO2. Electrochimica Acta, 281, 831-840.
Shinde, S. R., Apte, S., & Tiwari, A. K. (2023). Electro-chlorination technology for disinfection of drinking water: a patent landscape. Recent Patents on Engineering, 17(4), 26-45.