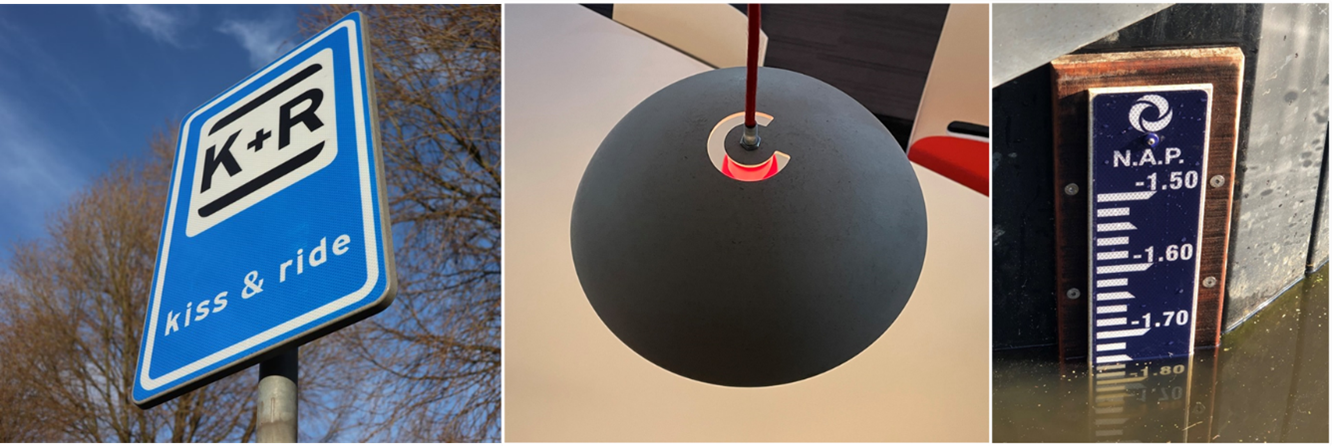
Description
Nabasco® 80xx circular thermoset bio composites are strong, dimensionally stable and light materials, suitable for various outdoor and indoor applications such as facade cladding, bank protection, signage, electronic housings and creative design. Nabasco® 8012 and 8020 specifically, are composed of waste fibres such as reed chips or cellulose flakes from WWTP screenings, recycled calcite granules from the drinking water softening process and a partially biobased polyester resin. These consist of more than 80% waste, have a low CO2 footprint and can be fully reused in new bio composite after a long lifespan. They thus offer a sustainable alternative to conventional materials such as hardwood, aluminium and glass composites. The materials require little maintenance and have a long lifespan and are produced both as sheet material (various thicknesses) and in free form moulded parts. In addition to the residual fibres, there are also Nabasco® materials available with other natural fibres (such as flax and hemp). All Nabasco® 80 materials have an aesthetic and natural appearance.
Images: Nabasco® 80xx series product examples: traffic sign, spherical design lamp, water level scale. See also Nabasco® 80xx series Facade cladding (listed separately)
Target audience
Owner of the product
Sign in to access this information.Actors, their roles and interactions
NPSP developed the materials and designs and produces products thereof in-house (the Netherlands) and with partners for B2B clients. All ingredients except the resins come from the Netherlands: calcite pellets from AquaMinerals (acting on behalf of its members, drinking water companies and water boards), cellulose fibres from Recell® (a specialised processor of such) and reed from a local reed cutter.
Unique selling points
Strong and light thermoset materials. Weather resistant, low maintenance. Reuse of water cycle residual flows. High material circularity index (>80% waste based, 100% recyclable). Low environmental impact (CO2 footprint). Long life span (>50 years). Freeform designability (moulded parts). Custom colours possible (>1000kg). Low-cost aluminium moulds possible. Sustainable alternative to hardwood, aluminium and glass composites.
Technical requirements
Products to be designed by or in collaboration with NPSP for manufacturing by NPSP and/or 3rd party. Process steps: 1. Application requirements 2. Form factor(s) 3. Suitable material composition and properties. 4. Parts design 5. Mould(s) design 6. BMC dough production 7. Biocomposite parts manufacturing 8. Finished Product.