Description
In this case study, Waternet, a full cycle water company, and NPSP, a front runner in biocomposites, have effectively collaborated to develop and produce biocomposite materials using raw materials from the water cycle and demonstrate them in various product applications. Raw materials found suitable for use were reed and grass fibres from the water board, recycled calcite from the drinking water softening process and cellulose fibres from WWTP screenings. From these, together with commercially available resins and fillers from agricultural waste, a range of thermoset Bulk Moulding Compound (BMC) materials have been developed with increasing bio and waste content up to 100%. At the end of their life span, these materials can be fully reused in their own production process, making them completely circular. The developed materials were subsequently applied and demonstrated in prototype products such as 3D facade panels, bank protection elements, nautical signs and water level scales, in a spherical design lamp and as a construction material in a weir, with the common goal of offering a sustainable alternative to less sustainable materials (such as aluminium and hardwood) currently used for these applications. An integral part of the work was to assess the health risks associated with using resources from wastewater and sustainability performance and commercial viability of the developed biocomposite materials and prototype products. The study was supported by TU Delft with research in the areas of health & safety and circularity & efficiency. Their contribution included leaching tests and associated environmental risk analyses for bank protection and facade applications and a methodology for the assessment and optimization of circularity and efficiency that was applied to the case. This case study proved the effectiveness of industrial symbiosis in upcycling water cycle residuals into marketable products and provided tangible demonstrations of circular use of those residuals in biocomposite applications.
Requirements and conditions
The development and production of bio-composites with natural and waste based ingredients and commercial positioning of these as an alternative to conventional materials posed challenges of a technical, operational and commercial nature. After all, a proven supply chain and partner ecosystem with critical volumes for these do not yet exist, where the conventional materials we want to displace are widely used with related efficiencies. A few requirements and challenges are highlighted below.
Requirement 1: Selected raw materials must be available and meet the required technical specifications for use in BMC composites, be clean, of consistent quality, and marketable in accordance with commercial and regulatory requirements (which implies that these are supported by relevant data and declarations, and not treated as mere waste).
Constraints:
- Natural and waste-based ingredients are not as pure as synthetic materials and their properties can vary according to the place of origin and seasonal influences, and for the natural fibres the weather conditions during growth and collection.
- Minimum processing and ordering volumes that often apply to raw materials, combined with best-before dates, can create barriers to scaling up new materials. These challenges can be managed, but they have an impact on costs and thus on competitiveness of the new materials.
Requirement 2: Developed biocomposites can be produced cost-effectively with reproducibly good mechanical properties as the minimum required for selected applications.
Constraints:
- The properties of natural waste fibres and bio-based resins are less than those of synthetic resins and fibres and related biocomposites may therefore require more material to provide comparable performance (as required by the product application).
- Producing bio-based and waste-based composites is technically more challenging than conventional composites, as the ingredients are less consistent and predictable, requiring more attention and tuning to make them work.
- The market volumes of bio-based and waste-based composites still need to scale up to achieve optimal chain and cost efficiency. The developed materials and products score on sustainability (because of bio and waste-based content and circular use), but lag on physical properties and cost per equal weight. With smart material-efficient designs, the price differences may be reduced in select applications, but not closed. A form of shadow pricing could stimulate the competitiveness and thereby upscaling of sustainable biocomposites.
Requirement 3: For wider uptake of the developed biocomposites, we will be looking for (volume) manufacturers who are willing and capable to work with the bio-based and waste-based materials.
Constraints:
- Established composite manufacturers show hesitant to use new bio-based and waste-based raw materials in their production process. These materials are not consistent batch over batch and are therefore potentially disruptive to a continuous production process. Moreover, this would lead to greater diversification in the sourcing of materials, resulting in associated costs and investments. To bridge this gap in the production and scale-up of the new materials, NPSP has taken up production itself, while continuing to pursue collaboration opportunities with other manufacturers.
Requirement 4: For a sustainable end product to be commercially viable, it must be considered feasible at scale to achieve a price within roughly 10% of comparable products that are demonstrably less sustainable and/or have a price differential that is fully offset by shadow prices for social and environmental impacts (i.e. be fully competitive on a true pricing basis).
Constraints:
- The new raw materials and biocomposites made thereof lack the technical and commercial reach with economies of scale that have been developed over time for conventional materials such as wood and aluminium.
- True pricing, applying shadow prices for environmental costs and social impact, can stimulate the introduction of biocomposites. Unfortunately, the sustainability value of bio-based materials is not fully recognized in the Environmental Cost Indicators (ECI), as the applicable Life Cycle Assessment (LCA) calculation rules (applied in the Netherlands) are such that long-term carbon sequestration in products does not count in the end-to-end carbon footprint.
- Although often demonstrably more sustainable, the use of bio-based composites is not (yet) widespread. A traffic sign with a base of biocomposite is more expensive than an aluminium traffic sign. Aluminium prices have been rising because of energy cost, but the production costs of bio-composites are equally impacted, moreover by the rising cost of labour.
Outcome of assessments
NPSP is developing LCA and EPDs for the new materials. In the Netherlands, to include a material in the ECI of a building, this material must be included in the National Environmental Database (NMD, 2020). This requires a standardized and often quite costly LCA study of the material. These can only be pursued for selected materials with sufficient technical maturity and potential. The carbon footprint analysis shows promising results, especially for the fully bio-based variants, which show negative kg CO2 eq when CO2 sequestration is included.
TU Delft performed a human health quantitative risk assessment based on Inductively Coupled Plasma Mass Spectrometry (ICP-MS) analysis for heavy metals and dangerous substances such as resin compounds (e.g., styrene and furfuryl alcohol) with QCRA and QMRA methods used in both deterministic and stochastic modes. Additionally, environmental quantitative risk assessment has been performed based on data collected during the laboratory leaching tests conducted at TU Delft and following the European guidelines for environmental risk assessment framework using the ratio PEC/PNEC to assess risks. Where PEC is the Predicted Effects Concentrations, represented by leaching tests results, and PNEC is the Predicted No-Effects Concentration, collected from ECHA (European Chemicals Agency) database. Then, a leaching-oriented Environmental Risk Analysis (ERA) for bank protection elements and façade elements made of new bio-composite materials were performed. These assessments took into account the environmental conditions for this, as well as leaching tests and other data. In the practical case, all leaching values remained below the applicable risk limits.
TU Delft developed a methodology for the assessment and optimization of circularity and efficiency. When applied to the case, it was concluded that the eco-efficiency of the production of 1 kg of bio composite is lower than that of 1 kg of hardwood, but that in application the eco-efficiency of 1 m2 of bank protection with bio composite is higher than that of 1 m2 with hardwood.
Key lessons
In all cases, residual flows must be processed into a usable and marketable product. This usually falls outside the core tasks and expertise of a public water utility and requires industrial partners who have the vision and ability to convert these residuals into marketable raw materials on a scale that is economically viable, and who accept the associated business risks and who can operate and develop the market for this. A starting point for the business model could be that residual flows are offered to the industrial partner free of charge, so that the water utility does not have to incur additional processing or disposal costs, which leads to cost savings for them.
During this project, NPSP realized that it would have to develop its own production capacity, because established dough producers and pressing companies are - for economic reasons - not keen to experiment with bio- and waste-based raw materials and because sustainability requires local production and the shortest possible supply chain. Since, NPSP has been increasing their BMC dough production capacity and their pressing capability. NPSP also started testing their dough with an established (EU) press company, for whom it will be a first experience with such bio- and waste-based ingredients. For NPSP it is their entry as a dough supplier, a specialty that needs development (evidenced by the fact that there are only a few of them in the EU, far less than press companies). Considerations about making and pressing dough in-house or outsourcing are not only an economic issue, but also affect the supply chain and consequently sustainability and delivery performance (the latter also due to non-harmonious implementations of waste legislation).
Legislation and policy recommendations
Relevant EU legislation, direct or indirect, includes: EU Green Deal, Circular Economy Action Plan (COM/2020/98 final), EU Waste Framework Directive (2008/98/EC), EU Urban Waste Water Treatment Directive (91/271/EC), EU Drinking Water Directive (2020/2184), EU Water Framework Directive (2000/60/EC), Single Market for Green Products Initiative including the evolving EN 15804:2012+A2:2019, product category rules (PCR) for Type III environmental declarations for construction products and services, and the EU policy framework on bio-based, biodegradable and compostable plastics.
Relevant national (NL) legislation and policies includes: the Environmental Management Act (Wet Milieubeheer), which includes NL implementation of the Waste Directive (ch.10), the Water Act (Water Wet), among others regulates water management systems and explains the tasks and organisation of the water authorities, the National Waste Management Plan (Landelijk Afvalbeheerplan (LAP), a policy framework for waste in the Dutch circular economy), the Green Deal Raw Materials Union of Water Authorities (Green Deal Grondstoffen Unie van Waterschappen, C‐174), which attempts to strengthen the economy while simultaneously decreasing the dependence on fossil energy and scarce natural resources by promoting and increasing the recovery of usable raw materials from wastewater, and the National Approach to Biobased Construction (Nationale Aanpak Biobased Bouwen, NABB), a stimulus program aimed at rapidly scaling up the market for biobased raw materials in construction, which - not coincidentally - includes SMART targets with regard to the processing of biobased materials in, among other things, road furniture and bank protection applications.
Applied products
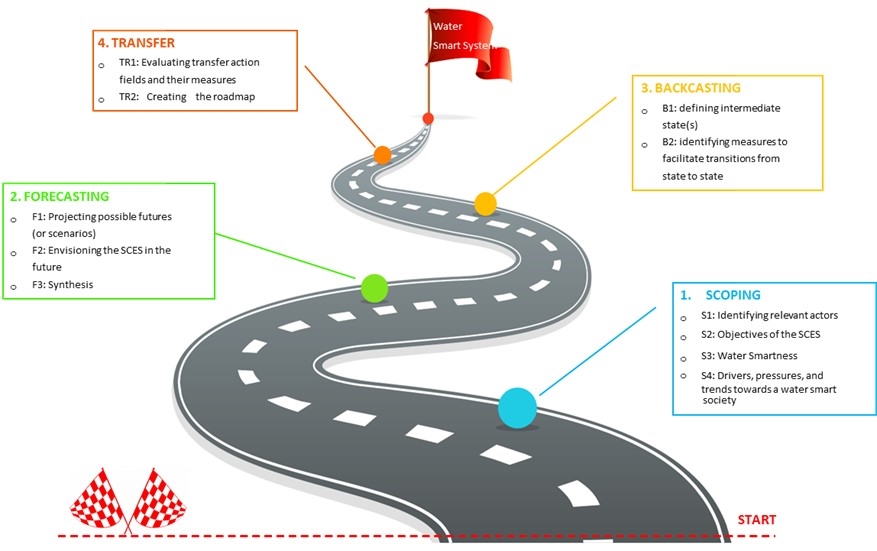
The WIDER UPTAKE roadmap guide
The WIDER UPTAKE roadmap guide, developed by the H2020 WIDER UPTAKE project, offers a comprehensive framework for imple…
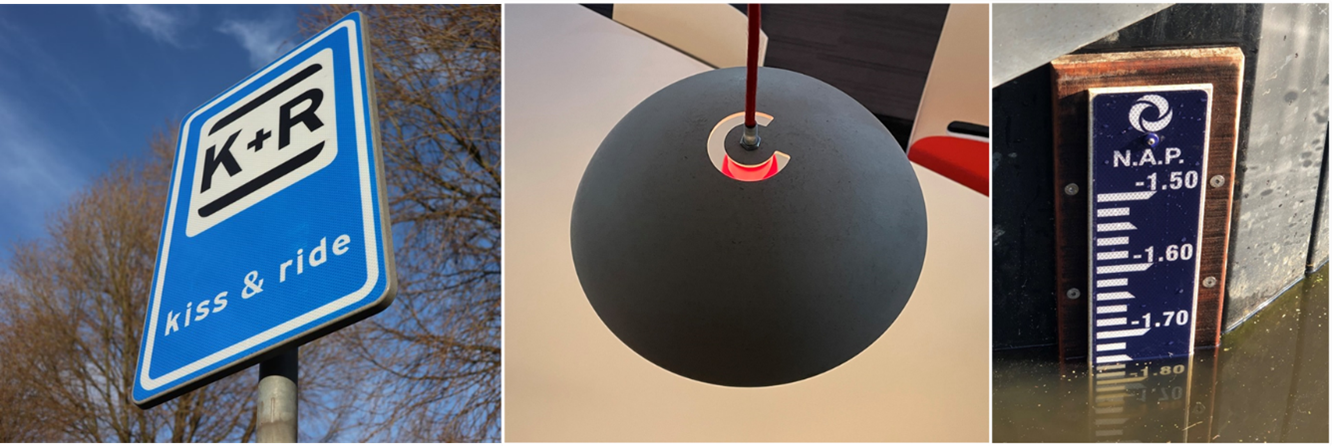
Nabasco® 80xx series bio composite materials
Nabasco® 80xx circular thermoset bio composites are strong, dimensionally stable and light materials, suitable for vari…
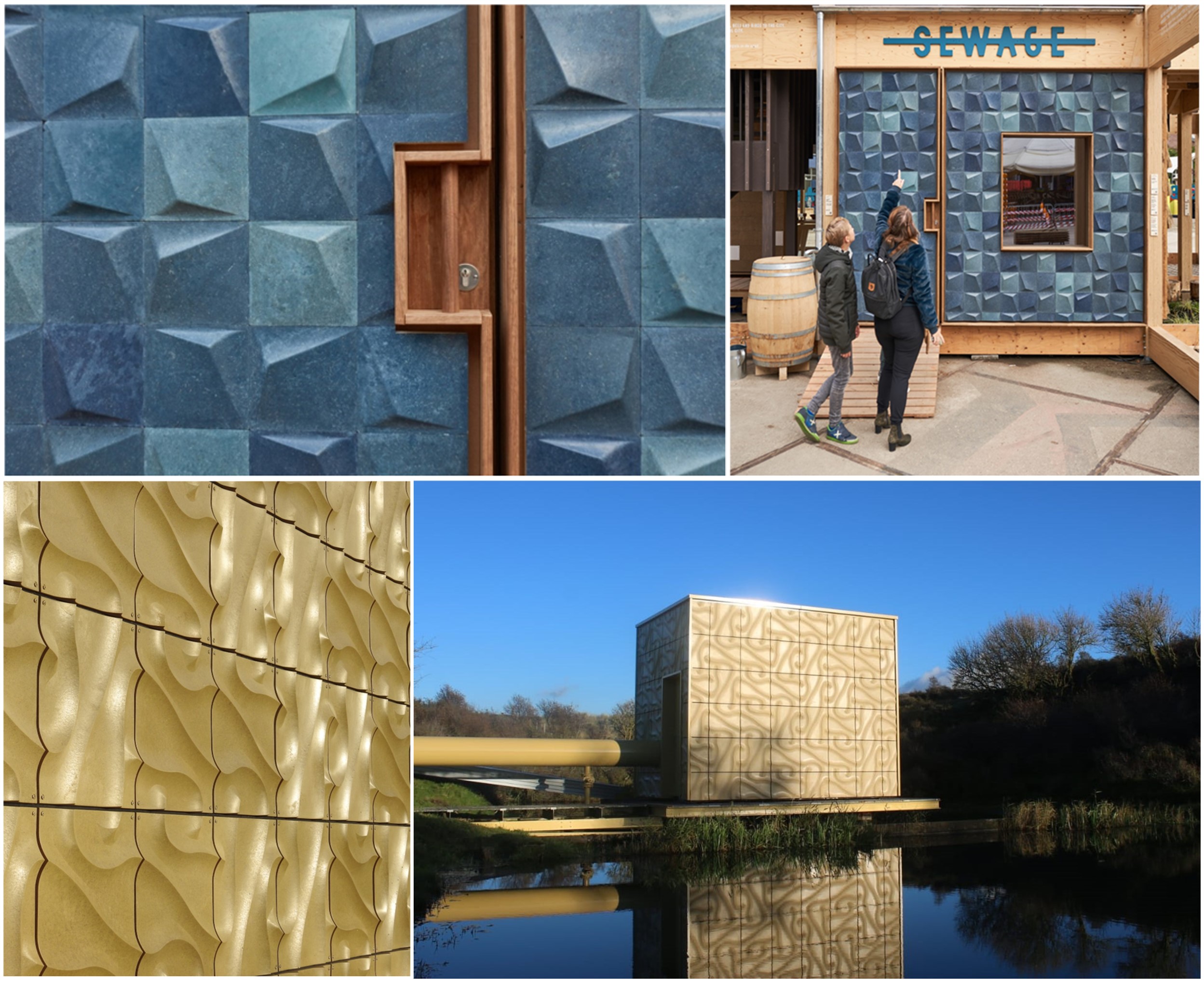
Nabasco® 80xx series Façade cladding
Nabasco® 80xx bio composite materials are durable and maintenance free, making them very suitable for demanding outdoor…