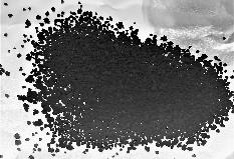
Unique selling points
- High quality product: renewable GAC
- Can be used for adsorption of contaminants from wastewater or polluted air
- Pathogen free
Description of the technology
Activated carbon is the collective name for carbonaceous adsorbents. Activated carbon is a non-hazardous, processed carbonaceous material with a porous structure and a large internal surface area (Henning et al. 2010). It can be produced from any carbon source (fossil, waste or renewable) and engineered to be used as sorbent to remove contaminants (Hagemann et al. 2018). Thus, activated carbon is capable of purifying wastewater via adsorption from contaminants such as phenols, acid dyes, pesticides and heavy metals. Also from polluted air, activated carbon can remove volatile organic compounds, nitrogen oxides and sulphur oxides. The efficiency of contaminants-elimination depends on the active surface, the porous structure, and surface functional groups of the activate carbon.
The combination of the pyrolysis with an activation process as presented here, aiming at the production of GAC, is usually applied in a side stream at wastewater treatment plants after digestion. Usually the process is implemented at wastewater treatment plants with a capacity of 100 000 population equivalents and greater. Most pyrolysis systems require dried biosolids in a granular form with a certain degree of uniformity in the material and low dust content (Metcalf et al. 2013). Therefore, the digestate is dewatered and dried. Together with other dried biosolids such as organic waste, the pre-treated digestate is pyrolyzed.
Pyrolysis and physical activation of carbons are typically conducted in two steps. During the first step, the carbonaceous precursor is pyrolyzed at temperatures between 200 and 950 °C in the absence of air (Metcalf et al. 2013, Smets et al. 2016). During pyrolysis, the volatile matter from the biosolids is removed and the biosolids are converted into a biochar characterized by a relatively high carbon content and a preliminary porosity. After pyrolysis, the carbon undergoes activation. The physical activation of the carbonized material consists of a partial and controlled gasification at high temperatures (i.e. 800 °C and 950 °C) with steam, CO2, air or a mixture of those (Plaza et al. 2014, Gergova et al. 1996, Rodriguez-Reinoso et al. 1995, Smets et al. 2016). During physical activation, the oxidizing gas removes the disorganized material, and eliminates the more reactive carbon atoms of the structure generating the porosity and contributing to the burn-off (Rodriguez-Reinoso et al. 1995)
If the two steps are combined, production costs can be reduced due to energy savings, a higher carbon yield, lower capital and operation costs as well as a lower processing time. In addition, a part of the excess heat resulting from the pyrolysis and the activation process is usually reused for the drying processes, while the other part contributes to the district heating. Finally, the activated carbon is granulated resulting in granular activated carbon.
Flow scheme of the technology
Pictures
Synergetic effects and motivation for the implementation of the technology
- Reuse of renewable GAC for tertiary treatment
The increasing population and demand for adequate sanitation lead to the increase in sewage sludge production. Furthermore, the current demand of advanced treatment processes for trace organic compounds elimination is the driver for transforming biosolids into GAC for tertiary treatment.
- Renewable GAC is a valuable and pathogen free product
Biosolids resulting from the sludge treatment at a wastewater treatment plant are processed further and converted into activated carbon which is a valuable and a pathogen free product.
Technology requirements and operating conditions
The parameters influencing the quality of the final product include the reaction temperature, the heating rate, the type of activation gas, the residence time and the content of total solids. The pyrolysis process requires a high content in total solids of at least 75% (Metcalf et al. 2013). Usually, the temperature for the process is chosen between 200 °C and 950 °C depending on the characteristics of the biosolids. High temperatures increase the surface area of GAC produced from digestates or biosolids, but decrease the yield of production (Inguanzo et al. 2002). The yield also decreases with increasing residence time at the same pyrolysis temperature (Zhang et al. 2015). Similarly, surface area and porosity are negatively affected by long residence time (Molina-Sabio et al. 1996, Lu et al. 1995).
The activation with steam is eight times faster than with CO2. Hence, lower temperatures can be used with steam than with CO2. In particular, the gasification with CO2 produces a larger volume of larger macropores, whereas the usage of steam leads to a larger volume of mesopores. CO2 is a mild oxidant at 800-900°C. Below 800 °C, the reaction velocity is so strongly reduced that the activation process ceases for all practical purposes (Henning and von Kienle 2010).
Parameter |
Units |
Min |
Max |
Reference |
Total solids |
% |
75 |
- |
NextGen D1.5 (in prep.), Metcalf et al. 2013 |
Reaction temperature |
°C |
200 |
950 |
NextGen D1.5 (in prep.), Smets et al. 2016 |
Heating rates |
K/min |
0 |
10 |
|
Residence time |
min |
10 |
120 |
Key performance indicators
Typical key performance indicators are the active surface quantified via the BET method (Brunauer et al. 1938), the porous volume, the hardness of the material and the bed volumes for a specific micropollutant removal rate depending on the empty bed contact time (EBCT). In the table typical ranges are shown for commercially available granular activated carbon as a reference.
Parameter |
Units |
Min |
Max |
Reference |
Active surface (BET) |
m²/g |
800 |
1200 |
|
Pore size distribution |
cm3/g |
0.307 |
2.127 |
|
Harndess of the material |
% |
95 |
99 |
Loreggian and Nättorp (2021) |
Bed volumes for 80% micropollutant removal |
BV |
9200 |
20000 |
Links to related topics and similar reference projects
Pyrolysis |
Reference |
GAC production |
|
Case Study applying the technology
Publications
- Brunauer, S.; Emmett, P. H.; Teller, E., Adsorption of Gases in Multimolecular Layers, 1938
- Gergova, K.; Eser, S., Effects of Activation Method on the Pore Structure of Activated Carbons from Apricot Stones, 1996
- Hagemann, N., Spokas, K., Schmidt, H., Kägi, R., Böhler, M., Bucheli, T., Activated Carbon, Biochar and Charcoal: Linkages and Synergies across Pyrogenic Carbon’s ABCs, 2018
- Henning, K., von Kienle, H., Carbon, 5. Activated Carbon. In Ullmann’s Encyclopedia of Industrial Chemistry, 2010
- Inguanzo, M., Domı́nguez, A., Menéndez, J., Blanco, C., Pis, J., On the Pyrolysis of Sewage Sludge: The Influence of Pyrolysis Conditions on Solid, Liquid and Gas Fractions, 2002
- Kleyböcker, A., Kenyeres, I., Poor-Pocsi, E., Nättorp, A., Loreggian, L., Schaub, M., Egli, C., Grozavescu, M., Murariu, M., Radu, B., Scheer, P., Lindeboom, R., Giurgiu, R., Suters, R., Heinze, J., Soares, A., Vale, P., Kim, J., Lanham, A., Hofman, J., D1.5 (2022) New approaches and best practices for closing materials cycle in the water sector, 2022
- Loreggian and Nättorp, Personal communication based on unpublished data, 2021
- Lua, A., A detailed study of pyrolysis conditions on the production of steam-activated carbon derived from oil-palm shell and its application in phenol adsorption, 2020
- Lu, G., Low, J., Liu, C., Lua, A., Surface Area Development of Sewage Sludge during Pyrolysis, 1995
- Metcalf & Eddy, Inc., Tchobanoglous, G., Stensel, H., Tsuchihashi, R. Burton, F., Wastewater Engineering: Treatment and Resource Recovery, 2013
- Molina-Sabio, M., Gonzalez, M., Rodriguez-Reinoso, F., Sepúlveda-Escribano, A., Effect of steam and carbon dioxide activation in the micropore size distribution of activated carbon., 1996
- Pelekani C., Snoeyink, V., Competitive adsorption between atrazine and methylene blue on activated carbon: the importance of pore size distribution, 2000
- Plaza, M., González, A., Pis, J., Rubiera, F., Pevida, C., Production of microporous biochars by single-step oxidation: effect of activation conditions on CO2 Capture, 2014
- Rodriguez-Reinoso, F., Molina-Sabio, M., Gonzalez, M., The use of steam and CO2 as activating agents in the preparation of activated carbons, 1995
- Sbardella, L., Comas, J., Fenu, A., Rodriguez-Roda, I., Weemaes, M., Advanced biological activated carbon filter for removing pharmaceutically active compounds from treated wastewater., 2018
- Smets, K., Jong, M., Lupul, I., Gryglewicz, G., Schreurs, S., Carleer, R., Yperman, J., Rapeseed and raspberry seed cakes as inexpensive raw materials in the production of activated carbon by physical activation: effect of activation conditions on textural and phenol adsorption characteristics, 2016
- Zhang, J., Liu, J., Liu, R., Effects of pyrolysis temperature and heating time on biochar obtained from the pyrolysis of straw and lignosulfonate, 2015